Hello everyone, today I would like to share with you the method of removing the surface knife marks of the processing marks left after CNC aluminum parts processing, as well as the influence of magnetic polishing machines in this industry.
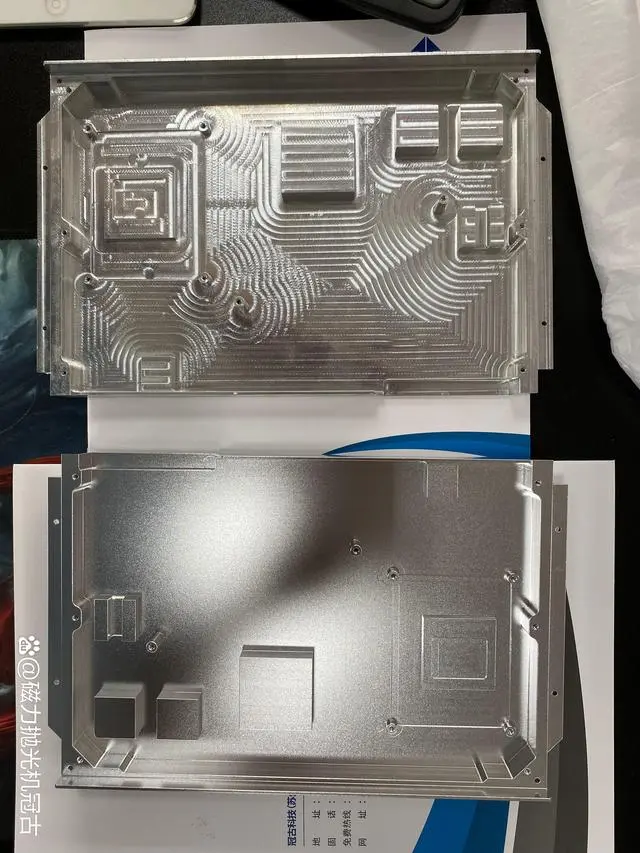
1.Manual polishing: This is the most traditional method, which uses sandpaper, abrasive paste and other tools to manually polish the surface. The advantage is that it can be finely controlled, but the disadvantage is low efficiency, which is suitable for small batches or workpieces with particularly high requirements.
2.Chemical polishing: Use chemical solutions to polish the surface of aluminum parts. Chemical polishing can achieve a higher surface finish, but it is necessary to strictly control the ratio and operating conditions of the solution, and pay attention to environmental protection and safety issues.
3.Mechanical polishing: Use a polishing machine and a polishing wheel to mechanically polish the surface of aluminum parts. This method is more efficient, but for workpieces with complex shapes, it may not be possible to polish evenly.
4.Electrolytic polishing: Polishing the surface of aluminum parts through electrochemical reactions, which is suitable for mass production and can improve surface finish and corrosion resistance.
5.Magnetic polishing: This is a more advanced polishing method, which uses the magnetic field to drive the magnetic abrasive to polish the workpiece surface. The advantage of the magnetic polishing machine is that it can evenly and quickly remove the processing marks and knife marks on the workpiece surface.
You must be logged in to post a comment.